階をまたぐ液漏れ・雨漏れなどの対策について紹介します。
化学プラントはストリップ工場が多いですが、一部には壁で囲われた建屋が存在します。
一般の建屋とは違って、化学プラントでは配管が建屋を貫通する形で配置される場合があります。
ここで漏れの問題が起きます。
屋上に配管が貫通する場合は雨漏りとして、屋根がある場所の下部では液漏れや粉体漏れが起こりえます。
雨程度だったら気にしなくてよくても、薬液が漏れてきたら大ごとですね。
上の階で漏れた薬液が下の階に落ちてきて、下の階で作業している人にかかってしまう悲劇が起こりえます。
こうした漏れを防ぐための具体的な方法を解説します。
一般論としてはコーキングや溶接によると言えますが、それでは具体的な指示が漏れてしまって液体や粉体も漏れる構造になりますよ。
階をまたぐ漏れを嫌がる理由
階をまたぐ漏れを嫌がる理由を最初に説明しましょう。
化学プラントはストリップで上からの雨や横殴りの風などが入ってくることを前提とした構造にしているはずです。
それでも嫌なものは嫌。
精神論のような気もしますが、実際にはちゃんとした理由があります。
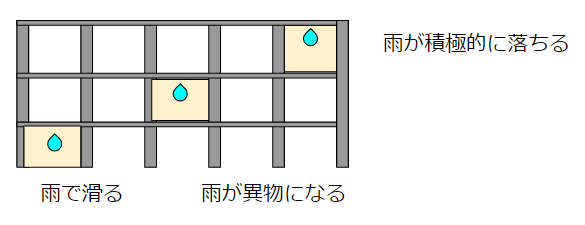
- 単純に嫌
- 異物になる
- 薬傷が起きる
- 滑る
単純に嫌
雨が落ちてくるというのは心理的に嫌なものです。
大したことない雨でも、傘をさしていないと下を向いて小走りに移動する人が多いですよね。
結果は大きくは変わらないはずなのに、少しでも濡れたくないという心理が働きます。
これは工場内でも同じこと。
雨が落ちてくるプラントで運転していると、雨漏れにすらお金を掛けれないケチな古臭いプラントという印象も出てきます。
雨漏れ対応はそんなに難しいものではないので、できるなら早めに解決したいですね。
異物になる
化学プラントで漏れを嫌がる最大の理由は異物でしょう。
雨が漏れる → 原料に水が混入する。製品に水が混入する
これらはどちらも製品品質に影響を与えます。
仮に綺麗な水であっても異物として扱われる場合もあります。
大気中の色々な汚れを含んだ雨なら言うまでもありませんね。
雨漏れ以外にも工場内で使用した水が排水溝を伝わずに、予期せぬ場所から下に落ちてきても異物になりえます。
薬傷が起きる
水漏れや粉漏れは作業員などへの薬傷のリスクを高めます。
水や粉を大気中で取り扱う場所は一般に壁で囲って部屋の形状にするでしょう。
囲い込みという表現をします。
外に拡散させないように囲い込んでいるはずが、下の階に漏れたら本末転倒ですよね。
綺麗な水で設備を洗浄して危険な薬液や粉体が付いた水が下の階に落ちたら、人に当たる可能性があります。
薬液の成分によっては薬傷に繋がります。
滑る
雨などが漏れると滑る可能性が高くなります。
TPMや安全管理という意味でも、リスクとなりえるものは排除したいと思うでしょう。
コンクリート床ならまだしも鉄板床なら水が付着していると確かに滑りやすくなります。
事務所などでも転倒事故が増えている現在では、工場では完璧な対応をしておきたいですね。
配管の貫通部
配管の貫通は化学プラントでの水漏れが最も起こりやすい部分です。
下の図を見てみましょう。
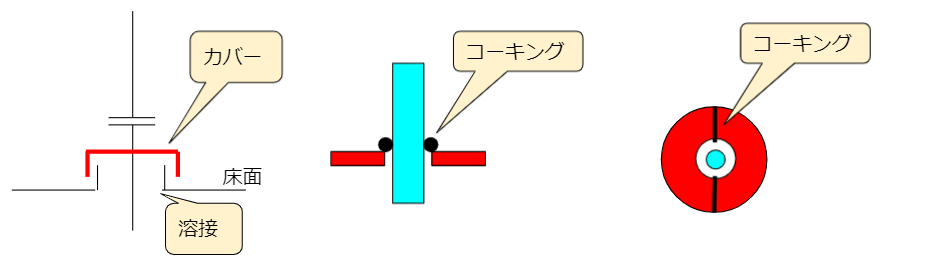
配管を貫通させるためには、床面に穴を開けます。
通常はフランジよりも大きい開口部にしないといけません。
開口部がある以上、床からの漏れを無くすために水切りを付けます。
開口部が配管外径よりはるかに大きいので、カバーも付けます。
水切りよりも大きなカバーのサイズにして、水切りがカバーの中に納まるように設計します。
これをそのまま付けたら終わり!・・・てはありません。
カバーと配管の間に必ず隙間ができます。
カバーは2つ割構造にする以上、すきまができます。
シリコンコーキングなどで防ぐといいでしょう。
シリコンコーキングは一度で完全に水漏れを防げるわけではありません。
雨のたびにチェックして晴れたらコーキングを施工していきます。モグラたたきのようですね。
設備の貫通部
設備の貫通部は配管の貫通と同じ発想です。
問題はその大きさ。
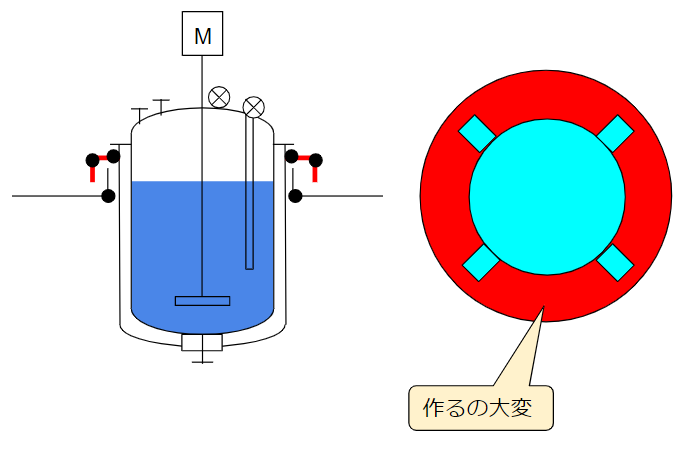
装置のサイズが大きいので製作その物が実は大変です。サイズ以外に
- 装置にブラケットが付いていて単純な円形穴ではない
- 吊り耳・ノズル・水切りなど干渉部も考慮しないといけない
- 作った後の再加工が難しい
という要素があり、予め作っておくということが難しい世界です。
概略の図面を予め提示していたとしても、実際には設備を設置して床が設置された後で、実寸をスケッチして製作することが多いでしょう。
時間も手間もかかってしまいます。
配管貫通部も状況は同じですが、サイズが大きいという点が厄介な要素です。
機械エンジニアにありがちですが、こういうカバーをいったん付けた後に改造するのは「チョットだけだから楽だろう」って思いがちです。
依頼元の製造部などはもっと簡単に依頼して来るでしょう。
でもこれは実は大きな勘違い。
結構大変なケースが多いです。
切って張ったを繰り返すと、溶接のひずみがあちこちに出てきます。
何となく綺麗な形に再加工できたように見えても、現地で付けようとしたら付かない・隙間ができた・・・というようなトラブルが頻発します。
この辺は難しいということをまずは認識して、施工会社とよく相談しましょう。
「簡単だろうから、すぐやってください」というような依頼の仕方は絶対にダメです。
脚の接続部
配管の貫通ほど多くはありませんが、脚の接続も問題になります。
配管ではなく機械設備の貫通というケースです。
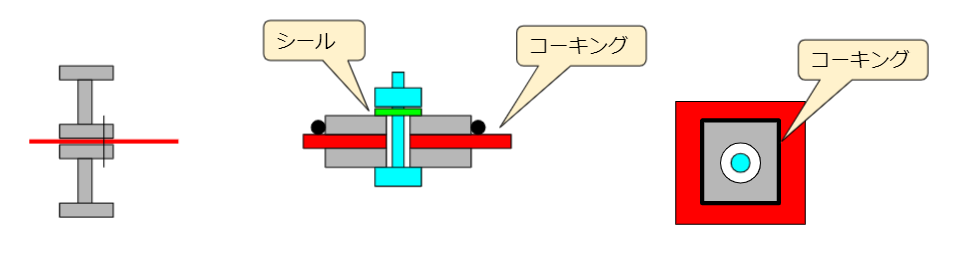
床面を挟んで、C型チャンネルやH鋼などを取り付けて、機械の荷重を建物の梁に受けようとします。
工事資料的には一番左の図のような、簡単な表現で終わってしまいがち。
ところがここには水漏れの場所が2つあります。
- ボルト貫通穴
- 床とベースプレートの間
見落としがちですよね。
事実、ほとんどのケースで施工されていません。
ボルトで締めているから漏れないだろう、床とプレートの接触面積が大きいから漏れてこないだろう。
こういう希望的観測に縋る形になります。
これでは隙間に雨や粉が溜まって、腐食が進みやすくなります。
対策としてはボルト貫通穴はコードシール系で、床とベースプレートの間はシリコンコーキングで埋めていきます。
床とベースプレートの間は、全周溶接で完全にふさいでも良いでしょう。
床と脚の切り離しの頻度は、配管の取り外しに比べれば圧倒的に少ないからです。
逆に配管は腐食したり切替工事をしたりする場合には、すぐに取り外せるようにするためにも、溶接は避けた方が良いです。
参考
最後に
化学プラントで雨漏れなど階をまたぐ漏れの対策について解説しました。
カバー・コーキング・溶接くらいしか方法はありません。
下の階に液や粉が漏れると、異物や薬傷の原因になったり転倒したりするのでできるだけリスクを下げるように取り組みをしましょう。
設備の開口対策は工事準備段階で念入りに確認が必要です。
化学プラントの設計・保全・運転などの悩みや疑問・質問などご自由にコメント欄に投稿してください。(コメント欄はこの記事の最下部です。)
*いただいたコメント全て拝見し、真剣に回答させていただきます。
コメント