Wireless diagnosis technology for pumps is gaining attention in industrial maintenance. But how effective is it really? This article explores the benefits, limitations, and practical considerations of using wireless systems to monitor pump health and performance.
Introducing articles from plantengineering.com.
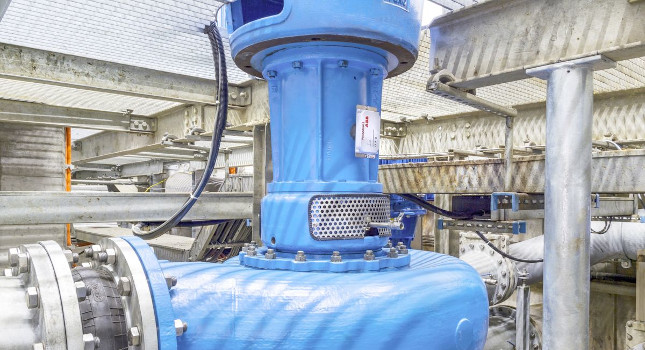
It is common to perform vibration diagnosis to extend the life of a pump.
Wireless diagnosis has become a hot topic these days.
Nowadays, it is becoming difficult to secure maintenance personnel, so we have no choice but to promote this.
However, there are a number of problems that need to be overcome in order to proceed with this.
expensive
Wireless diagnostics are expensive.
For chemical plant equipment that is constantly monitored, a diagnostic machine must be installed for each piece of equipment.
It costs money just to run a single power cable, but adding other measuring instruments is a cost in itself.
It is necessary to narrow down the number and compare it with the effort required by maintenance personnel.
It will be difficult to see the effects of introducing it unless there is a high demand for diagnostics, such as a large number of machines or a small number of maintenance personnel.
No complicated information required
If the problem is a pump, there is almost no need to diagnose the equipment.
For most pumps, you only need to check for vibration.
It is not necessary to carry out this diagnosis 24 hours a day, and it can be done by ordering it once a month.
The only difference is whether the period until inspection is required is one month earlier or longer.
Just because of this difference, you don’t need constant monitoring data, and you end up with excess data that you can’t utilize.
Temperature information is almost unnecessary as vibration alone can cover a lot.
Being able to do a variety of things does not necessarily make users happy.
Explosion protection issues
Wireless diagnostics have explosion-proof issues.
Wireless can be of great value for remote installations in non-explosion-proof areas.
In cases where equipment is concentrated in explosion-proof areas, such as in chemical plants, it can be said that the installation itself is difficult and the effectiveness is low.
LINK
Conclusion
Wireless diagnosis for pumps offers significant advantages for predictive maintenance but also comes with challenges. By understanding these factors and planning carefully, plants can improve pump reliability and reduce unexpected downtime.