Condition diagnosis is a vital maintenance strategy that helps detect equipment issues early and avoid costly failures. However, many hesitate due to concerns about the diagnosis cost. This article explains what factors influence the cost of condition diagnosis and why it is a worthwhile investment.
Introducing articles from plantengineering.com.
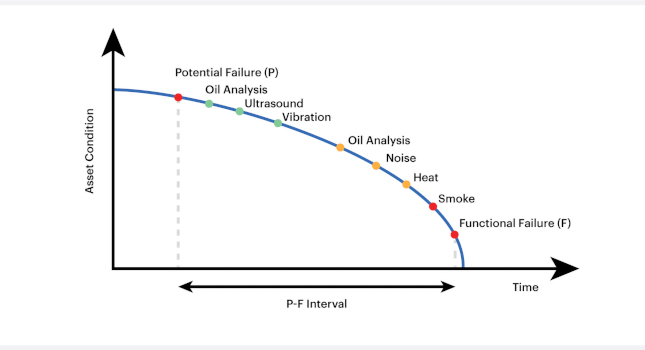
When we talk about plant maintenance, the topic of discussion is the advancement of condition maintenance.
Although it is understandable in theory, it is quite difficult to implement.
Explosion proof
If you try to use electrical power instead of human power, explosion-proof problems will inevitably occur in chemical plants.
It is not impossible to monitor the pump with various measuring instruments.
Chemical plants use many pumps, so it is difficult to attach a measuring device to every pump.
It will have to be limited to important pumps that are not in explosion-proof areas.
low human cost
Condition monitoring can be done by humans if continuous values are not required.
You can monitor the condition to some extent even at regular intervals such as once a month.
As long as the cost of human labor is lower than the cost of mechanization, constant monitoring will not become established.
On the other hand, if you are in an environment where it is not possible to allocate people for maintenance, you should not proactively use machines for monitoring.
Even with automatic monitoring, people still need to see it.
If an abnormality is detected during condition monitoring, manual repair or switching will be required.
Even if it is possible to automate a momentary changeover, repairs must be done by humans.
Even if only the diagnosis is mechanized, the effect will be low.
I think the scope of application will be wider if more analog equipment can be attached to the site to make judgments, rather than using electronic data.
Since the simplest method is to measure noise, I don’t think there is any point in creating another analog system…
LINK
Conclusion
Investing in condition diagnosis pays off by improving reliability and reducing unexpected failures. Understanding the cost structure helps companies plan and optimize their maintenance budgets.