Cooling systems are vital for maintaining safe temperatures in industrial plants. Proper calculations ensure efficient cooling and prevent equipment failures. This article covers the fundamental concepts and calculation methods for plant cooling systems, helping engineers and technicians understand and apply these principles effectively.
Introducing articles from plantengineering.com.
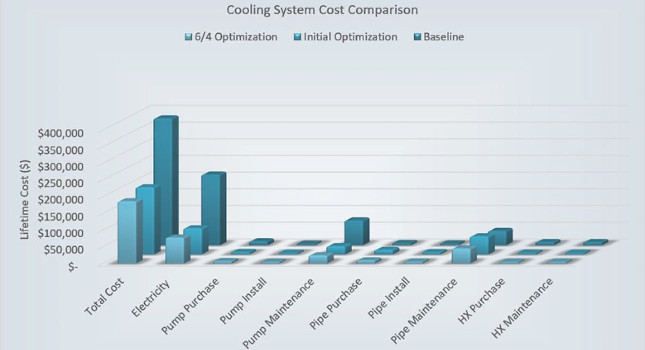
Chemical plants generate a lot of heat, so cooling systems are important.
When building a plant or introducing a new production item, cooling system calculations are required.
I will explain this basic idea.
Organize the main reaction heats
Thermal calculations come first in cooling system calculations.
It is important to calculate from a large part, and in the case of chemical plants, the heat of chemical reaction applies.
The heat of reaction can be calculated by multiplying the heat of reaction per unit quantity by the quantity handled and dividing by the required time.
Since it is an averaged amount of heat, it does not calculate the maximum heat load, but the calculation usually works out well.
Organizing operation time
Let’s clarify the relationship between reaction heat generation time and operating time.
The maximum heat load is calculated assuming that all reaction times occur simultaneously.
I think this is fine.
Some people may set the heat load to a value lower than the maximum value depending on the actual operating time.
The purpose is to reduce costs.
Refrigerators deteriorate as they are used, and I don’t think it’s a long-term idea to suddenly design them with less capacity that is not on the safe side.
Set margin rate
After calculating the heat of reaction, calculate some other amounts of heat that seem to be large.
This is necessary, but there is no point in calculating it in too much detail.
Since you will be setting a margin rate, you can omit it if the amount of heat is likely to fall within that range.
Setting the margin rate is extremely important and greatly influences the future prospects of the plant.
When calculating the amount of heat for single production in a single plant, even if the heat load was low at the time, the heat load may increase in the future.
If you’re going to spend a lot of money on it, it’s better to check your margins first.
Split into multiple devices
After setting the required heat load, let’s set the required number of refrigerators.
Even if you make a mistake, do not try to cover all the heat with one refrigerator.
If that machine breaks down, the entire plant will stop.
Think carefully about what to do in the event of a breakdown or power outage, and consider separately the minimum required cooling system maintenance and the cooling system necessary for operation.
Even if the cooling system is not at 100% capacity, shutting it down safely should be your top priority.
storage tank design
Calculate the cooling water tank capacity.
Calculate by adding the required equipment jacket capacity and piping capacity to provide a margin.
This does not apply when using seawater.
pump design
Calculate pump capacity.
Once the heat load per unit time is determined, the flow rate can be easily determined.
Once the flow rate is determined, the pipe diameter can be determined.
Friction loss can be determined from the piping diameter and layout, and the pump head can be determined.
Conclusion
Mastering the basics of plant cooling system calculations is essential for designing reliable and efficient cooling solutions. With proper understanding and careful calculation, plants can operate safely and cost-effectively.