プラントの自動化に欠かせないDCS(分散制御システム)は、多くの装置と機器から構成され、複雑に見えますが、その基本的なハード構成を理解することは制御技術者にとって重要です。
DCSは機械屋が関わることがないわりに、工場としては非常に重要。概要だけでも理解できていると、計装エンジニアと話をするときに理解しやすいかも知れませんよ。
この記事では、DCSの主要なハードウェア構成要素とそれぞれの役割を初心者にもわかりやすく解説します。プラント制御の基礎をしっかり押さえたい方はぜひご覧ください。
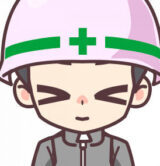
DCSの概要は制御と関連しているので、機械屋でも抵抗感ないかも。
DCSの体系図
DCSの体系図は下記のようにシンプルに表現できます。
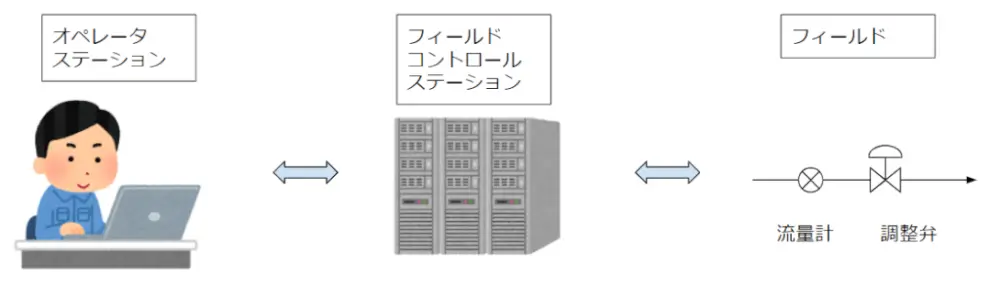
システムとしてはまずは現場があります。
この業界ではフィールドと呼びます。
この体系図ではフィールド部分が小さく見えますが、本当はフィールドは非常に大きいということを忘れてはいけません。
サイズ的にも運転の重要度的にも、です。
現場の信号を集積するステーションがあります。
I/Oラックもここに収まります。
人間が操作するステーションがあります。
HIS((Human Interface System)とも呼びます。
人間が情報を得て、操作するための部分です。
工場の心臓部として計器室があり、計器室の写真として写る場所はこの部分です。
いっぱいの机とモニターが集まっている場所ですね。
制御部分
制御部分は、I/Oラックも含めて以下の機能を持っています。
- プロセス演算を行うCPU
- フィールド信号をデジタル信号に変換
- 制御変換されたデジタル信号をフィールド信号として返す
下記のようなフィードバック制御を行うというイメージでいいです。
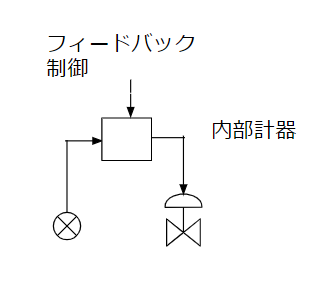
極端に言うと、ここまでで制御としては完結しています。
人間が存在しないで運転ができるなら。
操作監視部分
人間が操作監視する部分はどうしても必要です。
その部分を構成する要素は下の図のようなものです。
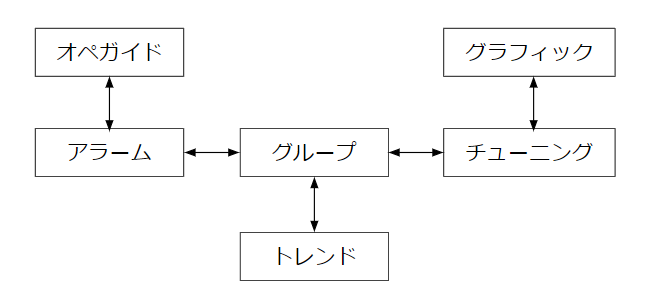
DCSのHISには下記の機能があります。
- グラフィック
- オペガイド
- アラーム
- トレンド
- チューニング
- グループ
この中でも、よく見かける画面がグラフィック
フロー図と必要な運転値の情報が表示されています。
運転状況を総合的に監視する部分で、HISの肝です。
トレンドも非常によく使います。
複数の指示時の時間応答をグラフにするものです。
運転解析には必須。
このトレンドは機械屋も使用するべきです。
オペガイドでは特殊な運転状況を言葉で表示してくれます。
アラームは言葉どおり警報。運転の異常を教えてくれます。
この辺は運転上の重要なポイント。
多くの情報を同時処理するうえで、監視が疎かになる部分も、アラームが教えてくれます。
アラームが多すぎて、運転員のストレスになるという問題も出てきており、最近はアラームの設定も重要な課題になっています。
「いつ何が起こったか」を記録検証するときにも使えます。
チューニングやグループは、運転の臨時的な状況で使うことが多いです。
運転開始時のPIDパラメータ調整や、運転時の手動介入などに使います。
ここは勝手に変えてしまうと、運転条件は簡単に変わります。
その意味で非常に重要であり、危険な場所と言えます。
キュービクル・ネスト・カード
ステーションはいわゆる直方体の形をしているイメージでしょう。
ですが、実際にはステーションは機能名であり、実物名を指しているわけではありません。
電気室などで見かける盤はキュービクルと言います。盤でも十分通じます。
キュービクルはいくつかの棚段になっています。
この棚段それぞれネストという箱があります。
このネストの中に、カードというプリント基板を入れます。
カードの種類
ステーションの最小単位としてのカードを見てみましょう。
下記のようなイメージです。

ネストという箱の中にカードがいっぱい入っています。
このカードは、例えば温度計の指示信号用に1つ、温度計の制御信号用に1つというように、割り当てがされます。
カードの役割としては大きく3種類
- 信号分配用
- 入出力用
- 制御用
フィールドから指示値が入力され、その信号を制御用に変換し、変換した信号を制御部に分配する。
機能の分類
信号の各種変換を行う機能をカードは持っています。
それぞれの機能に分けてカードを設定するのは、カードの機能を統一化するため。
1点の温度制御だけを考えれば、ここまで複雑に組み上げる必要はありません。
複数の制御を1つの場所で効率的に行うために、機能を分配するという方法を取ります。
機能の分類の例としては以下のようなものがあります。
- アナログ/デジタル
- 入力/出力
- 温度制御情報/その他プロセス流体
- アラーム
- インターロック
それぞれの機能ごとにステーションを作り、キュービクルの中に、ネストを配置し、カードを挿入していく。
こうすると、整理しやすいという発想です。
これは会社と同じですね。
- 本社支社
- 製造部/事務所
- 営業/研究/販売
- 広報
- 経理
- 人事
機能ごとに事業所・部署を作り、部署の島を作り、机を割り当て、作業をする。
制御 | 会社 |
ステーション | 事業所 |
キュービクル | 部署 |
ネスト | 机の島 |
カード | 作業者の机 |
誤解や反論を招きそうですが、カードが机・ネストが机の島という点が、非常に似ているということを言いたいです。
信号の入出力
私が理解に時間がかかったというのは、下の図を教えてくれる人がいなかったから、という単純なものです。
この図はプロセス計器から信号を検出して、制御値をプロセスに返すまでのハード面の体系を示しています。
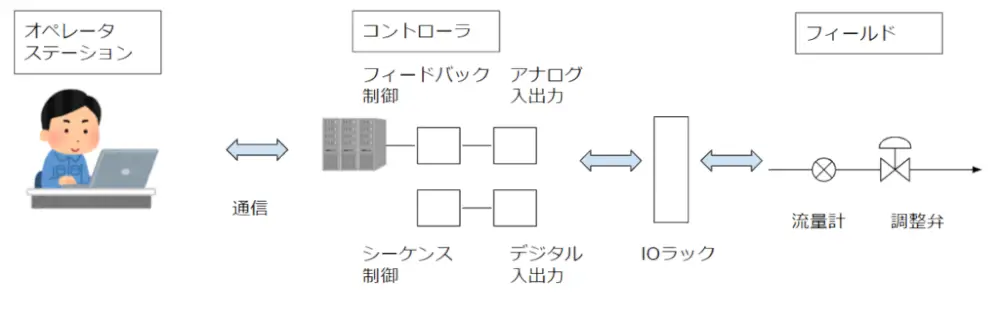
アナログ計器
アナログ計器の例として、温度制御を考えましょう。
温度制御をお子あうためには、下記の動作を行います。
- 温度計の指示値を検出
- I/Oラックで温度の電気情報を信号情報に変換
- コントローラのフィードバック制御で制御値を決定
- I/Oラックで信号情報を制御情報に変換
- 制御情報値を調整弁に伝達、作動
I/Oラックや入出力カードは専門的な単語なので、極端な話をいうと知る必要はありません。
デジタル計器
デジタル計器もアナログ計器と同じように説明が可能です。
デジタル計器としては液面計によるオーバーフロー防止が分かりやすいでしょう。
原料をタンクに共有していて、タンク液面が一定値になれば、原料供給弁を閉めるというシーケンスです。
- 液面計の指示値を検出。
- I/Oラックで液面の電流情報を信号情報に変換
- コントローラのシーケンス制御で制御値を決定
- I/Oラックで信号情報を制御情報に変換
- 制御情報値を調整弁に伝達、作動。
アナログ制御はPIDによるフィードバック制御がターゲットですがシーケンス制御にも活用します。
デジタル制御はフィードバック制御には使わず、シーケンス制御で使うのが普通。
信号の入力
信号の入力は、I/Oカードを介すると記載しました。
そこをもう少し見ていきましょう。
下の図を見てください。
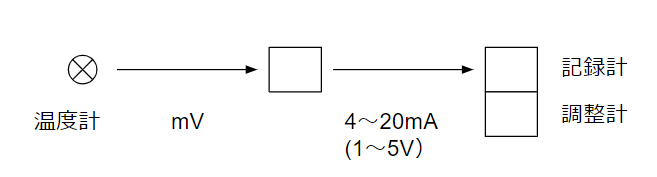
温度計の指示値をmVの単位の電気情報として発信します。
温度計としては抵抗温度計などをイメージしてください。
これをI/Oカードで、制御用の信号に変換します。
DC 4~20mAが一般的です。
mV単位の温度に関する電圧情報を、4~20mAの伝送情報に変換するための電気回路があり、そこにDC24Vを供給している。
それくらいの理解で十分でしょう。
これより先は、電子回路の話になりますので・・・。
この信号をフィードバック制御に使用したり、記録用に使用します。
信号の出力
信号の出力は、入力の逆と考えれば基本的にはOKです。
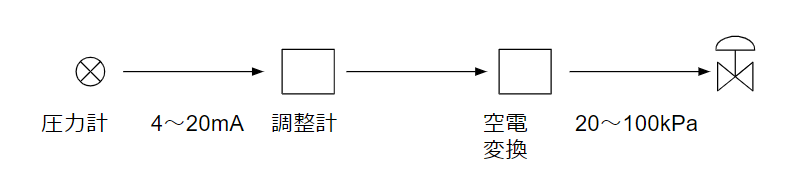
出力の最終計は、計装空気の圧力になります。
計装空気の圧力で、調整弁の作動位置を決めるため、
DC4~20mAの電気信号を、空気圧力に変換するための電空変換器が必要です。
I/Oカードなどと同じく、信号の変換場所と理解していれば十分だと思います。
電気と空気
DCSと現地を結ぶ信号の伝達方式は電気と空気があります。
空気は昔の技術と考えて良いです。
ノズルフラッパーとか相当原始的な技術です。
現在では電気がほぼ全数を占めています。
空気と電気の信号という意味での比較をしておきましょう。
電気 | 空気 | |
伝達速度 | 速い | 遅い |
演算 | かんたん | 難しい |
記録 | かんたん | 大変 |
精度 | 高い | 低い |
故障予測 | 難しい | かんたん |
空気は故障予測がしやすいという点くらいにしかメリットがありません。
それも空気配管中の閉塞がいつ起きるかは気が付かないかも知れないですし、圧力変動の方が課題です。
自動弁の数が増えて圧縮エアーの消費量も増えているので、計器の信号伝達に対して空気を使うというのはリスクが高いでしょう。
指示・記録・警報
制御のメインの流れが上記のとおりだとして、サブ的な機能の中に指示・記録・警報などの要因があります。
指示計
指示計というと現地にセットする場合が多いです。
DCSでも指示をすることは可能ですが、そこまで重要でない情報の場合に、現地にセットします。
この需要は、年々減っていっています。
私は詳細は知りませんが、DCSの能力が上がっているからだと信じています。
もしくは、現場での作業がどんどん削減していることや、現場とDCSとでのコミュニケーションのやり取りが高度化していることが原因にあるのでしょう。
いずれにしても、需要のない指示値を示すためだけに、スタンションを立てることは、プラントの省スペース化に反した流れですので、今後なくなっていくでしょう。
記録計
これもDCS化が進んだ現在では、個別に分けて意識する人は少なくなっています。
昔の記録紙の時代を知っている人は、記録計の存在も意識しているでしょう。
記録を電子データでなくて、紙で行うためには、情報を紙に出力するためのアナログな装置が必要です。
これがサブ的な要因として概念上は今でも存在します。
記録計の存在がなくなり、DCSで何でも済ませようとすると、関係者以外の人から見ると
- DCSがあるからデータは無限に格納が可能。
- サーバーの容量が無限にあるからデータを無限に収集が可能
こういう風に勘違いする人は、必ず出てきます。
警報
これも年々需要は減っていっています。
DCS内にある警報をソフトアラーム、DCSとは別に警報盤で表示する警報をハードアラームと区別したりします。
サブ的な要因として提示する警報は、ここではハードアラームのことを言います。
DCSでもアラームを発信することができ、DCSで制御をかけるときには、ソフトアラームも制御の一部と考えられます。
一方、ハードアラームはDCSの信号は使っていますが、DCSとは別に強調して表示する場合が多いです。
もしくは、DCSに取り込まない機器の警報情報を表示する場合でしょうか。
よくある例が冷凍機などの特殊機器です。
冷凍機は制御盤をローカルに配置し、その範囲内で完結させることが普通です。
冷凍機の情報をDCSに取り込まないことも多いでしょう。
取り込んでも電流値だけということが多いです。
そこで異常が起きた時には、現場で警報が鳴りますが、それでは気が付きにくい。
その警報情報をDCS室に移送する場合、DCSのソフトアラームで発砲するのではなく、ハードアラームで表示する方が楽です。
DCSの設定をしなくて済むからですね。
電源
電圧と聞いて、日本で思いつくのは家庭用の100V電源でしょう。
100V電源なんて使っている国はほとんどありませんが。
化学プラントでは440V電源が主流です。
昔のプラントで220V電源の場所もあります。
計装用電源は100V以下
さて、今回のターゲットである計装用電源は100V以下がほとんどです。
220Vや440Vの電源は、私の中では高い電圧と認識していますが、それは100Vの家庭用電源になれているから。
計装用電源が100V以下であるいうのは、計装用電源に高い電圧が必要でないから、
という読み取ることもできます。
計装用電源はDC24Vが多い
計装用電源は100V以下の中でも特に24Vがほとんどです。
電流で4-20mAという単語を聞いた人はいるでしょうか?
機械屋が耳にする機会は少ないので、意識していないと耳に入ってこないかもしれませんね。
4-20mAはアナログ計器の信号として使います。
具体的には以下のものがあります。
- 液面計・温度計・流量計などの連続的な信号
- 調整弁の開度調整などの連続的な指示
アナログ信号なので、AI/AOと言われます。
アナログ信号は4-20mAの電流です。
20mAと言えば、感電すればかなり危険な値です。
自動弁の開閉は100Vが多い
計装用設備の制御機器と言える自動弁。
この自動弁には100V電源を使用することが多いです。
一般的なカタログには、100V・200V・24Vをラインナップしていますが、100Vを基本にしていることが多いようです。
電磁弁とリミットスイッチに使うだけであり、どちらの設備も上記の電圧で使えそうです。
100Vが多いのは、日本で汎用的だからでしょうか。
いずれにしろ、汎用的な仕様を選ぶのが正しいので、100Vが多いと思っていればいいと思います。
これはon-offのように0-1で決まる信号のやり取りに使います。
on-off自動弁がその典型例です。
化学プラントで使う計装設備の大半はon-off自動弁です。
これはできるだけ汎用化させたい。
一方、特殊なものが4-20mAのアナログ信号。
アナログ信号をAI/AOというのに対して、on-off自動弁などのデジタル信号をDI/DOと言います。
二重化
二重化とはどういう意味でしょうか?
言葉どおり同じ設備を2個持つことを意味します。
普通の設備は1個しか持ちません。
それなのに、同じ設備を2つ保有するのはなぜでしょうか?
故障したときの影響が大きすぎるから
というのがその答えです。
DCSは各計器の信号をいくつかの装置に集合させて処理しています。
そこで重要な部品が壊れると一瞬で全てが使えなくなる場合があります。
アナログ計器であれば、仮に壊れてもその計器が使えないだけであり、運転を継続させようと思うと、何とか可能です。
そこがDCSの弱点。
DCSでは二重化という単語がいくつも出てきます。
その部品を個々に確認していきましょう。
制御ステーションの二重化
制御ステーションは、制御装置の心臓部。
化学プラントの心臓部であるDCSのさらに心臓部。
ここが壊れたら確実にアウト。
ですので、制御ステーションは2重化します。
CPU、メモリーの二重化
制御ステーション内のCPUや目盛などの重要部品はさらに二重化します。
制御ステーションが壊れるのは最悪。
その最悪の一歩手前で止まるようにする
というのは化学プラントの安全運転の基本思想です。
電源の二重化
電源も当然のように見えますが二重化します。
電源装置が止まると、停電でなくても、装置全てが動きません。
カードの二重化
I/Oカードも二重化します。
特に制御用の入出力カードは二重化します。
自己診断機能
これらの二重化部品は、壊れたかどうかを人が判断するのは、合理的でありません。
大昔はパトロールで定期的にチェックしたかもしれません。
ですが、今では自己診断機能を有した電子部品が一般的。
当然ながらDCSもその自己診断機能を持っています。
自己診断を行い、異常があれば警告を出し、予備に切り替わる。
これが普通でしょう。
切替作動
二重化をしていても、片方がずっと動いていて、他方が止まっていては、動いていない方の設備を急に動かしても動かないかもしれません。
動かしていないから故障しているのかどうかが分からない。
こういう問題が起こりえます。
そこで、二重化をする設備は基本的に
定期的に動かす設備を切り替える
ということをします。
工場内の機械設備なら手動で切り替えないといけませんが、
DCS内の部品なら、自動的に切り替わるのが普通。
DCSとシーケンサ
DCSの話題が出た時にシーケンサの話題も当然出ます。
機械屋としてはこれをハードの面から見た方が理解しやすいでしょう。
DCS
DCSは通常、ユーザーの工場計器室に設置しています。
そのプログラムは工場の制御担当者、もしくは外部の制御エンジニアが作成します。
そのプログラムの制御対象は、工場の設備。
工場を動かす上で自動化が必要な設備を、全てプログラムに取り込みます
これは自前作成の範囲。
DIY(Do It yourself)と言ってもいいでしょう。
バッチ系化学プラントでは、ほとんどがこの自前作成です。
というのも、制御らしい制御があまりないからですね。
DCSに取り込む計器の信号点数はAI/AO/DI/DO合計で1000〜2000点くらいあります。
この中で制御らしい制御、比率制御やカスケード制御などを使っている点数は100点いかないと思います。
単独のPID制御を含めても300〜500点の範囲内でしょう。
つまり、50%以上は単なるon-offのデジタル開閉や定値制御です。
簡単な制御はすでに方法が確立されていて、記号を合わせるだけの組み合わせゲームです。
特殊な制御にのみ、知恵を絞らないといけません。
自前作成をするということは、標準化をできるだけすすめ、特殊なところを減らすという作業でもあります。
シーケンサ
さて、バッチ系化学プラントではその制御は極めて簡単と言っています。
これまで制御で対象にしているものは、ほぼ全て配管中の弁や計器類の話です。
機械屋としては装置の制御はどうなっているか疑問に思いませんか?
実はほとんどの設備は、極めて簡単な制御しかしていません。
制御が必要な機器とは回転機です。
その回転機の制御は動かす。これだけです。
- 動かすか動かさないか
- 動かす速度をどれだけにするか(インバータ)
複雑な機械は非常に数が少ないです。
例えば遠心分離器。例えば冷凍機。
こういう設備の制御プログラムを自前作成することはしません。
普通はメーカーに依頼します。
ここでメーカーはシーケンサを使ってプログラムを作ります。
それを制御盤に設置して、メーカーの制御盤とユーザーの制御盤を接続します。
こうしてメーカーの制御盤とユーザーの制御盤の間で、信号の授受を行い、制御します。
ややこしいものは外出し!
最後に
DCSのハード構成は多様な装置から成り立ち、それぞれが役割分担しながらプラントの自動制御を実現しています。基本構造を理解することで、システムの設計やトラブル対応がスムーズになります。この記事を通じてDCSのハードウェアの全体像をつかみ、実務に役立ててください。
化学プラントの設計・保全・運転などの悩みや疑問・質問などご自由にコメント欄に投稿してください。(コメント欄はこの記事の最下部です。)
*いただいたコメント全て拝見し、真剣に回答させていただきます。
コメント