化学プラントで使う範囲でPIシステムについて解説します。
DCSを持っているプラントではPIシステムも導入していることが多いと思います。
特に大きな工場では必須レベル。
機械系エンジニアとして実際どれくらい使っているかを解説します。
端的に言うとほとんど使っていません。
色々理由はありますが、プロセスエンジニアに解析を丸投げで依頼してしまっています。
える範囲がどれくらいのもの
DCSとの違いとして機械エンジニアが知っておくべき範囲でまとめました。
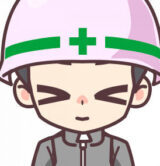
運転データが読めるようになると、設計の検証手段が増えて質を上げることができます。
DCS
DCSではプラントの運転データを一元監視できます。
圧力・温度・流量・液面などについて、化学プラントの各設備の情報を集約します。
このデータはどれくらい保管可能でしょうか?
DCSシステムで完結している系だと、そのシステム内のデータサーバのみです。
データサーバと言っていますが、要はパソコンですね。
パソコンのHDDやSSDの容量そのもので、格納できるデータ容量が決まります。
これだと不便なことが多く存在し、それを解決するためにPIシステムがあります。
PIシステム
PIシステムとはPlant Information Systemの略です。そのまま。
PIシステム上は、データをヒストリデータと呼びます。
この単語は使わず、プロセスデータで統一します。
プロセスデータの保存
PIシステムの最大のメリットは、データの保存量の拡張です。
DCSシステムをPIサーバと繋ぐことで、DCSのプロセスデータをPIサーバに移行することが可能です。
サーバの容量を増やしていけばいくほど、データを保存することが可能です。
PIサーバが無い場合は、1年程度の情報しか保存できないことがほとんどです。
USB等の外部メディアに手動で転送しなければ、一定年数を越えたデータは都度削除されてしまいます。
過去のプロセスデータは非常に貴重な財産ですので、捨てるのはもったいない!
プロセスデータの解析
プロセスデータを保存する目的は何でしょうか?
当然ですが過去のデータを未来に活かすためです。
合理化・安定運転などのために活用します。
化学プラントの中でも、バッチ系化学プラントでは切替運転を行うため、1年間に十分な運転データが得られない製品が存在する可能性があります。
1年間で2か月程度しか運転しないこともあります。
1年前くらいの運転状況なら、製造部の管理者も記憶していますので、その時との比較をすることは運転管理として一般的に行います。
そのためにも、過去のデータは必要です。
SDM終了後に生産再開する場合の、DCSのパラメータはSDM前の安定運転時のデータを使うことが一般的です。
この安定運転時のデータが1年より前になりうるのが、バッチ系化学プラント。
だからこそ、データの保存は重要度が高いです。
プロセスデータの共有
PIシステムを使えば、工場LANとデータをリンクさせることが可能です。
DCSが設置されている計器室以外でデータ解析が可能、というのがPIシステムのすばらしいところ。
製造部管理者が計器室で執務することは少なく、別の事務所で執務することが多いです。
この製造部管理者が、計器室に行かなくても事務所で運転データを取得できる。
これは管理者としては大きなメリットです。
工場とは離れた位置にある研究所などでも、工場のデータを瞬時に読み取り解析することも不可能ではありません。
事故やトラブルが起きた時に、現地指揮本部などの計器室外で情報を集めるためにも大活躍です。
私も結構お世話になっています。
チャンピオンデータの取得
機械系エンジニアがPIを使うときは、チャンピオンデータの取得がメインとなります。
- 温度や圧力の最も厳しい値を拾って、設計条件とする
- トラブルが起こっている箇所の、一番悪いケースを拾う
これを日々のバッチデータから拾い上げていくという、地道な作業が起こります。
データ的にはDCSのような短時間のサンプリングデータではなく、1分程度のデータしかないため精度は高くありません。
何となく傾向を知るためという使い方になるでしょう。
本当に細かいデータを知るにはDCSを見たり、オペレータに話を聞かないといけません。
この意味で、機械系エンジニアがPIを使って真剣に検討するというのは、あまり価値がありません。
対外アピール
PIシステムを使うことの意義は、対外アピールにあるように思います。
何かしらトラブルがあった時に、それを上に報告。
ここで目に見える運転データを見せると、上は意外と安心します。
もちろんPIの弱点をちゃんと知っていて、運転の実際を知っている人は騙されません。
そうではない一般の人には、データを使ってかっこいい解析をしているという錯覚を与えることができます。
そこにも一定の意味はあるでしょう。
解析能力不足
ところが、PIシステムの活用は十分には進んでいないことが普通です。
理由は簡単。
解析者の能力不足
1年前のデータを解析に使うといいつつ、バッチ工場で2か月分程度の運転データから特定のデータを抽出するのですら意外と大変です。
1日1バッチとして、60バッチ分のデータから数個のデータを選ぶからですね。
ヒストリデータのトレンドを60個程度流し読みして、該当しそうなデータを調べ出す。
地道で時間のかかる作業です。
手動介入の履歴が分からない
バッチ方式の運転では手動介入がそれなりの頻度で行われます。
ここで、なぜ介入したかが分からないという致命的な問題が起きます。
背景を含めたログが取れません。
どんな操作をしたのか(自動弁をいつ開けたとか)は分かっても、なぜそれをしたのかは作業者の判断に委ねられます。
引継ぎを疎かに考えるプラントほど、この問題は大きいです。
どれだけシステムを構築しても、最終的には人。
連続運転のように人が介在しないシステムを作る方がよっぽと健全な気がします。
もしくはバッチだから深く考えても仕方がないとあきらめてしまうか、作業者にカメラを付けて就業中の作業をすべて記録を取るか・・・。
参考
関連記事
関連情報を知りたい方は、以下の記事をご覧ください。
最後に
PIシステムが当然の時代にいれば、その恩恵にあずかってしまって思考停止してしまいがちです。
システムが便利になることで発生する弊害です。
歴史が重要ということは、年が経つほど感じますね。
化学プラントの設計・保全・運転などの悩みや疑問・質問などご自由にコメント欄に投稿してください。(コメント欄はこの記事の最下部です。)
*いただいたコメント全て拝見し、真剣に回答させていただきます。
コメント